Несколько лет назад Россия столкнулась с дефицитом продуктов на прилавках магазинов не из-за недостатка товаров, а из-за логистических проблем. Разработчики экосистемы прикладных научно-исследовательских центров «СИБУР ПолиЛаб» под руководством Константина Вернигорова помогли предотвратить этот сценарий. Впереди у них новые амбициозные планы.
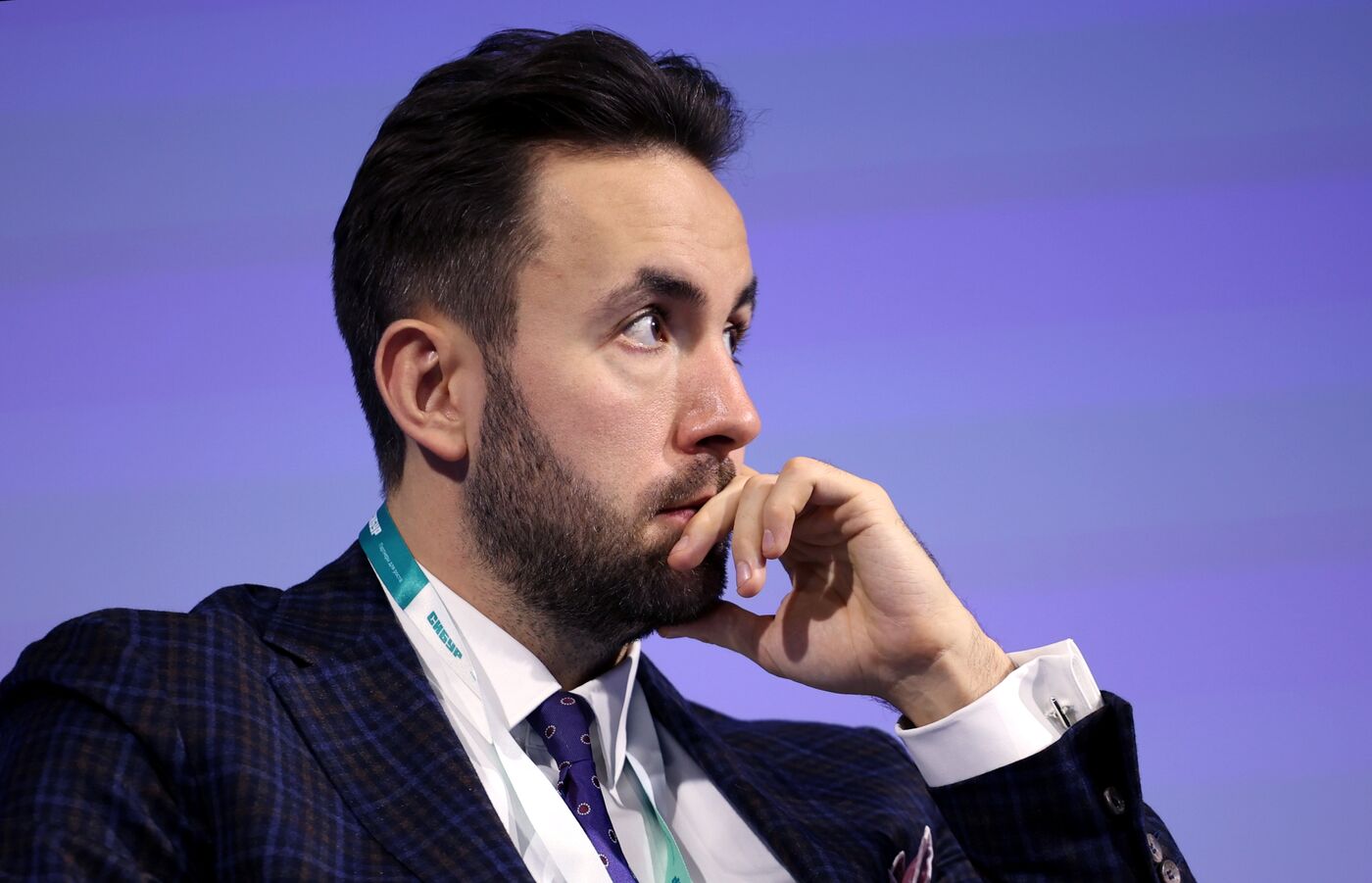
Naked Science: До вас мы беседовали Что разграничивает инновационные исследования и систему «ПолиЛабов»? Можно ли найти запоминающийся пример таких работ за последнее время?
Константин Вернигоров: При разработке кардинально новых технологий или инновационных молекул работу ведет «СИБУР Инновации». Когда продукт начинают производить значительными партиями на пилотных установках, а тем более серийно на промышленных — от десятков до тысяч тонн в год — задачи модификации продукта для нужд рынка, его правильного развития и позиционирования в конечном изделии и применении уже берет на себя «СИБУР ПолиЛаб». Именно поэтому всё это называют прикладными исследованиями и разработками.
Существуют суперконструкционные пластмассы, выдерживающие экстремально высокие температурные и механические нагрузки. Из них производят детали автомобилей и самолетов, применяют в медицине. Один из таких материалов — полиэфиркетонкетон, перспективный и высокоэффективный материал. Первый этап — получение собственной технологии его производства, этим занимается «СИБУР Инновации». После запуска в серию мы займемся доработкой материала под требования конкретного заказчика.
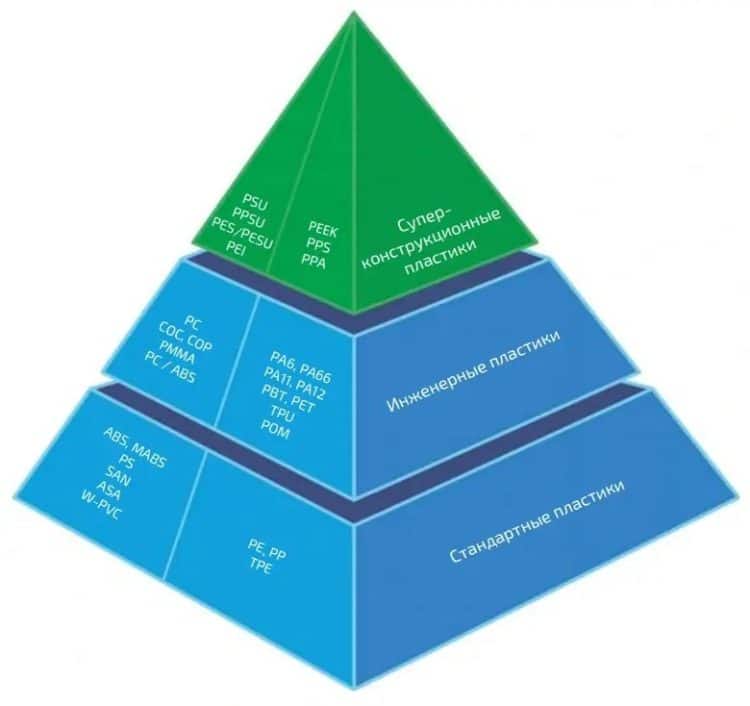
У специалистов компании «ПолиЛабы» большая загруженность – производит она сотни марок полимеров разных видов. В связи с этим, в компании функционирует множество центров разработки: семь, каждый из которых специализируется на определённой категории продукции.
Как организована работа по доводке новых продуктов в «ПолиЛабах»?
К. В.: Наша компания с давних пор изготавливает поликарбонаты и полиэтилен для сельского хозяйства.
Поликарбонат можно применять вместо стекла, не только в теплицах, но и в архитектуре, декорировании. Для успеха в конкретных применениях необходимо учесть множество нюансов. Например, поликарбонат должен быть устойчив к царапинам, иначе это повлияет на внешний вид и светопропускаемость. Какой смысл в легком и не хрупком замене стекла, если оно станет плохо пропускать свет? Важно также учитывать горючесть материала: в архитектуре разрешены только негорючие и трудногорючие материалы.
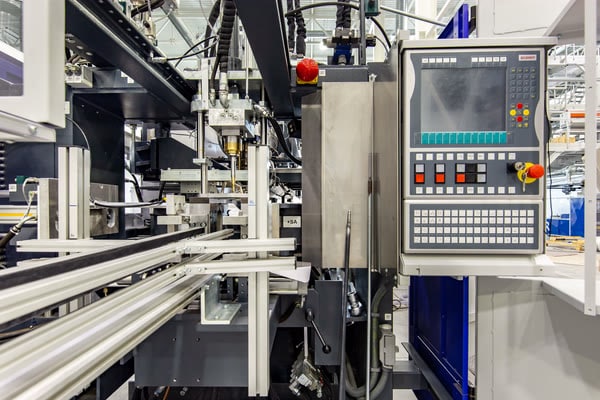
На арене появляются «ПолиЛабы». Нужно изменить материал, чтобы он соответствовал потребностям клиента. Удалось создать устойчивый к царапинам поликарбонат и повысить коэффициент светопропускания этого пластика — в итоге из него стали делать автомобильные фары.
Часто встречающаяся проблема любой уличной поверхности, от рекламного баннера до пластиковых дорожных заградительных панелей, защищающих от шума трассы, — граффити. С помощью наших «полилабовских» добавок удалось минимизировать адгезию краски к поликарбонату, и обычная вода легко удаляет нанесенную на поликарбонат краску.
В сельском хозяйстве полиэтилен применяют как укрывной материал. К нему предъявляются противоположные требования: он должен удерживать тепло, для чего необходимо блокировать часть инфракрасного излучения, но одновременно пропускать часть спектра ИК-излучения.
Без этого не вся солнечная энергия будет доступна растениям, эффективность их фотосинтеза ухудшится. «ПолиЛабы» разработали полиэтилен, пропускающий необходимую часть спектра, что ощутимо улучшило урожайность, в отдельных случаях её рост измеряется десятками процентов.
С 2022 года многие российские компании столкнулись с задачей импортозамещения. Что пришлось пережить «ПолиЛабам»? Были ли в практике случаев помощи партнёрам в экстренном замене критически важного импорта? Или может, самому приходилось экстренно импортозаменять что-либо?
К. В.: Импортозамещение — обширный термин, объединяющий разноплановые виды работ. С одной стороны, это обеспечение технологической независимости отечественных производств. Например, для нефтехимии критичным является доступ к катализаторам и специализированной химии. В этом контексте «ПолиЛаб» проводил исследования в двух направлениях: тестирование аналогов из дружественных стран и продвижение собственных разработок, которые велись в научно-исследовательских центрах СИБУРа.
Замена катализаторов и специальных компонентов — всегда точная настройка. Простое замещение одного компонента другим не гарантирует результата: требуется адаптация технологических режимов и комплекс испытаний, подтверждающих соответствие качества и эффективности полученного продукта. Производства обеспечены собственными разработками. Цель — полная самообеспеченность отечественными разработками к 2030 году.
Другая сторона импортозамещения — мы предлагаем решения не себе, а отраслям: разработка новых марок синтетических материалов в качестве замены ушедшим решениям.
Пример — поликарбонат для автомобильных фар.
N. S.: Можете привести еще примеры?
К. В.: Упаковка «тетра-пак» занимает третину всех молочных продуктов в магазине. Также её используют для детского питания, соков и других напитков.
Многие полагают, что тетрапаки изготавливаются только из картона. На самом деле внутренний слой каждой упаковки — это слой полиэтилена, нанесенный методом скоростной ламинации. До 2022 года этот полиэтилен был исключительно импортным.
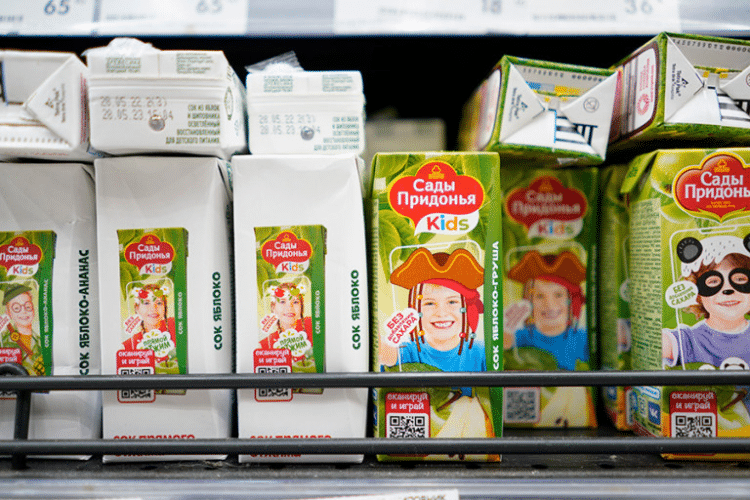
Другой пример – маркировки полимеров для медицины. Из них производят одноразовые шприцы, скафандры медицинского назначения, упаковку для лекарств. Всё это разработано и запущено в производство.
Устойчивость производства дала возможность предпринять следующий шаг и быстро удовлетворить запросы важных отраслей — строительства, транспорта, медицины, сельского хозяйства, пищевой промышленности и потребительских товаров.
С февраля 2022 года по конец 2024 года на рынок вышло более 80 наименований продукции.
Значит, до введения ограничений у вас не было этих наименований, из которых можно было всё это производить?
К. В.: Активно применялся многими производителями, но часть приходилось завозить из стран, ставших недружественными. Использование нового материала, новой марки полимера, всегда требует производственных переходов.
Я помню, как мы оперативно выполняли просьбы партнеров о замещении многослойных пленок для пищевых продуктов. Без них еда не дойдет до потребителя. Замещали и индустриальные пленки, без которых многие промышленные товары невозможно произвести в срок. В таких изделиях обычно применяют комбинацию полимеров в разных слоях. Для замены требуется не просто поменять один полимер, а всю комбинацию: каждый слой отвечает за определенные свойства.

С весны 2022-го по конец 2024 года выполнили полторы тысячи клиентских запросов. Запросы касались импортозамещения марок полимеров и получения технической консультации по эксплуатации оборудования.
Наша команда, работавшая над этим направлением, отличалась высокой степенью вовлеченности. Также отмечу редкую для нас открытость с партнёрами на всех этапах производства – от сырья до конечной продукции.
Получилось так, что сильные внутренние разработки помогли СИБУРу оставаться на плаву, а может быть, и расти во время санкций?
К. В.: Наш рост абсолютно очевиден, и в будущем он продолжит увеличиваться благодаря новым инвестициям. Амурский газохимический комплекс на 2,7 миллиона тонн полимеров в год, ДГП-2 В Тобольске реализуется ряд проектов, помимо производства почти на 600 тысяч тонн полипропилена.
Н.С.: Вы говорили об автомобилестроении, а оно совсем недавно ставило вопрос о проблеме пластмасс — точнее говоря, АБС-пластикИз него производят бамперы и другие изделия. Встречали ли вас такие случаи?
К. В.: Сегодня потребление полимеров в автомобилестроении выросло на 24%, что свидетельствует о высоком спросе на эти решения. К 2028 году использование полимеров в российском автопроме может удвоиться, а доля отечественных материалов достигнет 80%.
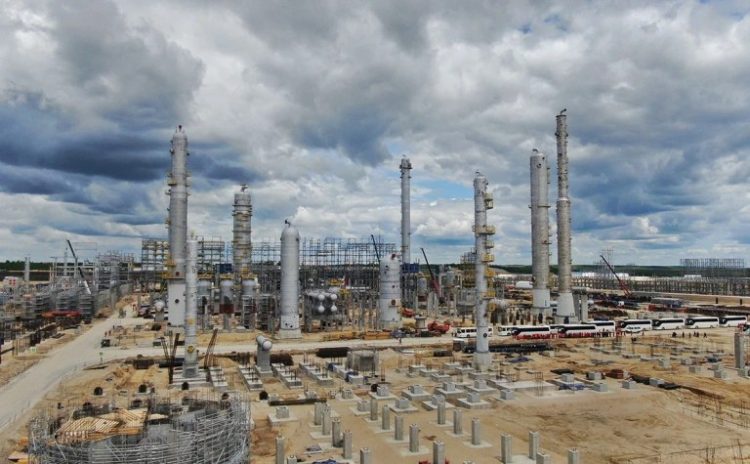
Много организационных деталей: сертификация, получение разрешения на внедрение материалов в производство автомобиля.
Система «ПолиЛабов» СИБУРа имеет десятки проектов по внедрению новых материалов в транспортную отрасль. Некоторые из них уже применяются отечественными автопроизводителями. Разработки идут быстро: поликарбонат для линз фар — один пример. АБС-пластик, валидированный для интерьерных деталей, обладает потенциалом для электротранспорта благодаря сочетанию прочности, теплостойкости и устойчивости к ударным нагрузкам.
В декабре СИБУР закончил строительство этиленового комплекса ЭП-600 в Нижнекамске. Запуск увеличит мощности «Нижнекамскнефтехима» по производству этилена и его производных вдвое, что откроет новые возможности для проектов импортозамещения современных синтетических материалов, таких как АБС-пластики, полистирол и новые марки полиэтилена.
N. S.: Как именно вы работаете с отраслями?
К. В.: В СИБУРе 11 отраслевых дивизионов глубоко погружены в потребности своих отраслей и могут предлагать партнёрам решения, отталкиваясь от поставленных задач. Хочется лучше понимать партнеров и клиентов, совместно развивать рынки, предлагая не только продукты, но и комплексные решения, которые открывают новые возможности для отраслей, общества и бизнеса. К таким отраслям относятся транспорт (пластиковые детали для автомобилей и многое другое), сельское хозяйство, гибкая упаковка, жесткая упаковка, медицинские изделия, строительство и другие.
В каждой из этих отраслей сохраняется большой потенциал для замены импортных решений, более экологичных и энергоэффективных вариантов, а также расширения использования уже существующих продукции. Эти меры способствуют росту местных производств во многих сферах.
Проекты, направленные на использование вторичных материалов в производстве, выделяются отдельно.
Н. С.: Как именно «ПолиЛабы» занимаются переработкой уже использованных пластиков? В последнее время часто говорят о том, что вторичный пластик, добавляемый в новый, — это уловка, ведь он снижает качество конечного продукта: молекулярные цепочки у добавленного «вторичного» материала короче. По этой причине многие люди считают бессмысленной сортировку и раздельную утилизацию пластиковых отходов. Существует ли опыт вашей компании, подтверждающий это или же при определенной пропорции вторичный пластик вполне оправдан?
К. В.: Многие исследования демонстрируют, что основные технические характеристики полимеров сохраняются на высоком уровне даже после многократных циклов переработки. Полиэтилен высокого давления (ПВД) и полиэтилен низкого давления (ПНД), полиэтилентерефталат (ПЭТФ, из которого производятся пластиковые бутылки) и полипропилен (ПП) уже сейчас широко подвергаются вторичной переработке.
Проблема не в переработке, а в ее недостаточном объёме. В России сейчас перерабатывается лишь 10-12% пластиковых отходов. Доля переработки должна увеличиваться. В СИБУРе инвестируем в технологии многократного использования современных синтетических материалов для производства конечных изделий.
Мы разрабатываем собственный инновационный бренд полимеров, включающий переработанный пластик: Vivilen. В рамках бренда предлагаются решения для упаковки как пищевых продуктов (Vivilen rPET с содержанием вторичного пластика до 30%), так и непродовольственных товаров (Vivilen rPO — с долей переработанного пластика до 70%).

В рамках этого бренда за 2024 год создали 16 новых марок, всего их более 80. Например, марка rPET обеспечивает потребление и переработку 1,7 миллиарда пластиковых бутылок ежегодно, что равно 34 тысячам тонн. С 2022 года компания перевела производственные цепочки 25+ партнеров на продукцию из материалов с содержанием вторичного пластика.
В научно-технологическом плане это лишь начало пути. Для возможности использования переработанного пластика важно его правильно сортировать. Поэтому проводим просветительскую деятельность: рассказываем о важности и правильности сортировки отходов, а также разрабатываем возможность строительства установки термолиза для химического рециклинга пластиков – технологии, позволяющей перерабатывать смешанные полимерные отходы.
При термолизе, химическом разложении при нагревании, пластиковые отходы распадаются на исходные углеводороды, аналогичные тем, которые получают при переработке нефти и используемые для производства обычных пластиков. Развитие этой технологии может сделать цикл переработки потребительских отходов из пластика практически бесконечным. Термолиз разделит молекулы на фрагменты, а мы соберем из них полимеры заново.
Николай Степанович спрашивает: ваше мнение о биоразлагаемых полимерах? В настоящее время по этой теме много информации, а некоторые утверждают, что они на самом деле не биоразлагаемые. Проводятся ли в этом направлении работы в России?
К. В.: Существование биоразлагаемых полимеров, например, полимолочной кислоты, подтверждено. Их биоразлагаемость установлена сертифицированными методами. Их можно использовать.
Всё это имеет смысл только при наличии полной системы. Например, в Европе есть контейнеры для раздельного сбора мусора: в одном — пищевые отходы в пакетах определенного цвета, которые опускают в соответствующий отсек. В другие отсеки выбрасывают пластик, стекло и так далее. Эти пакеты изготавливаются из биоразлагаемых полимеров. Компании, занимающиеся сбором мусора, отделяют их и вывозят на специальные полигоны компостирования. Там пищевые отходы вместе с пакетами превращаются в компост.
Часто «биоразлагаемым» называют пакет, изготовленный с использованием оксодобавок, позволяющих ему распасться на мельчайшие частицы и исключающие возможность повторной переработки. На российском рынке доля действительно биоразлагаемых пакетов не превышает 1-2%. Переработка же требует специальной инфраструктуры сбора и утилизации, которой в России нет. Смешение таких пакетов с обычными не позволит правильно переработать ни первые, ни вторые.
Производство биоразлагаемых пластиков составляет 10 миллионов тонн в год, а общее производство пластиков сотни миллионов тонн. Такое различие неслучайно. Помимо сложностей, о которых я уже говорил, существует существенная проблема — экономика: биоразлагаемые полимеры значительно дороже обычных.